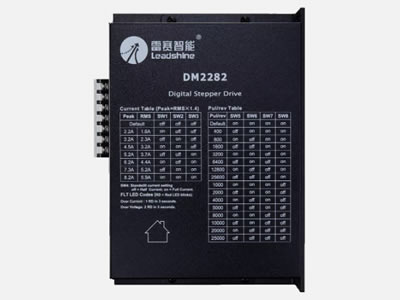
Leadshine DM2282 Stepper Motor Driver
1.200 KHz max pulse input frequency
2.8 output current settings of 1.4-8.2A via DIP Switches, or 0.5-8.2A via software.
3.16 microstep resolutions of 200-25,600 via DIP switches, or 200-51,200 via software
This Products is available in stock.
This Products is available in stock.
This Products is available in stock.
we will ship the package within 48 hours after the buyers pay momey by paypal
it is made in China Shenzhen Leadshine Technlogy Co.,Ltd ,100% original,
Leadshine DM2282 is DM2282 is a high voltage, versatility fully digital stepping driver based on a DSP with advanced control algorithm. It brings a unique level of system smoothness, providing optimum torque and nulls mid-range instability. Motor self-test and parameter auto-configuration technology offers optimum responses with different motors and easy-to-use. The driven motors can run with much smaller noise, lower heating, smoother movement than most of the drivers on the markets. Its unique features make the DM2282 an ideal solution for applications that require low-speed smoothness.
Features:
Step & direction (PUL/DIR) or CW/CCW (double pulse) control
150-230 VAC supply voltage
200 KHz max pulse input frequency
16 microstep resolutions of 200-25,600 via DIP switches, or 200-51,200 via software
8 output current settings of 1.4-8.2A via DIP Switches, or 0.5-8.2A via software
Configurable control command smoothing for reducing motor vibration.
- Original Leadshine.
- Working voltage: 150 - 230 VAC or 212 - 325 VDC.
- Anti-resonance function provides optimum torque and guarantees stability at medium speeds
- Motor self-test and auto-setup
- Multi-stepping technology allows a low input pulse frequency from which many small output steps are generated for smoother motor running
- Soft-start without "twitching" at power-up
- Output current selectable in seven steps via DIP switch, stepless via software
- Input frequency up to 200 kHz
- Inputs TTL compatible and optically isolated
- Automatic current reduction (in idle mode) to reduce motor heat; function can be switched off (percentage of current reduction can be configured via software)
- Suitable for 2-phase and 4-phase motors
- Supports PUL / DIR and CW / CCW operation modes
- Undervoltage protection, overvoltage protection, overcurrent protection, phase fault protection
Characteristic data | Min | Typ. | Max | Einheit |
Output current | 0.5 | - | 8.2 | A |
Supply voltage | 80 | 230 | 252 | VAC |
Logical signal levels | 7 | 10 | 16 | mA |
Input frequency | 0 | - | 200 | kHz |
Insulation resistance | 500 | MΩ |
Application:
The stepper motor is connected to the output stage via 4 lines. The output stage has 2 inputs for step and direction, the driving control supplies signals to these inputs, a pulse to "Step" to move the motor one step forward, at the same time a signal to "Direction" to determine the direction of the motor. Each motor needs its own output stage.
The supply voltage for the motor is connected to the output stage, 48V is recommended, because this way you get the best performance out of the motors.
The output stage can be adjusted to the motor in many ways, you have to set the maximum allowed current as well as the number of steps for one revolution. Thanks to digital technology, you can take half-step (400) here to still let the motor run silky smooth.
The output stage can be adjusted to the motor in many ways, you have to set the maximum allowed current as well as the number of steps for one revolution. Thanks to digital technology you can take a half step (400) to let the motor run silky smooth.